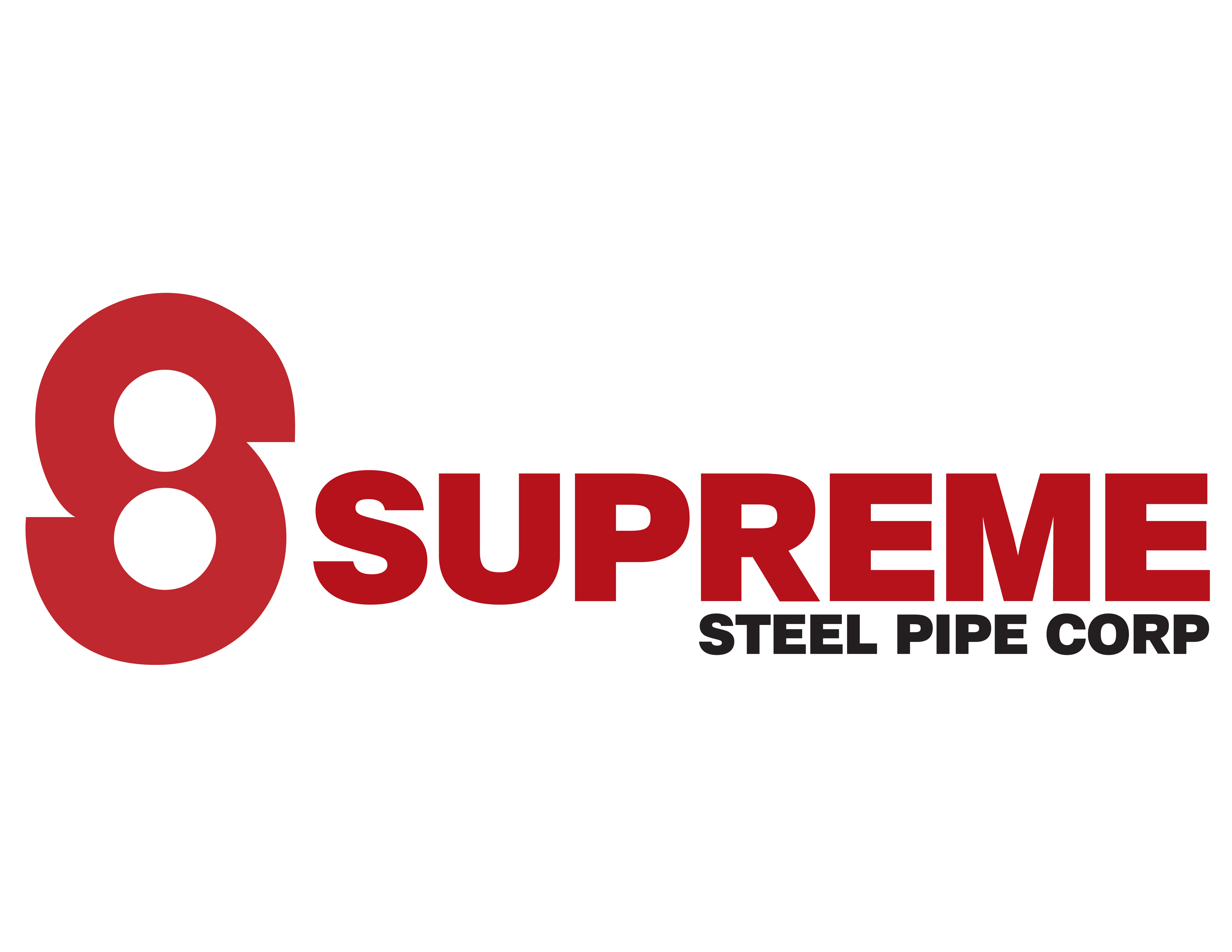
How Pipe Size Affects the Cost of Black Iron Pipes
How does pipe size affect the cost of black iron pipes?
- Material costs
- Manufacturing and logistics
- Supply and demand
- Installation costs
- Application efficiency
Overview
- Understanding how pipe size can affect the cost of black iron pipes is crucial for making cost-effective decisions in construction and industrial projects.
- The size of black iron pipes influences costs across various stages, including raw material pricing, manufacturing processes, logistics, and installation.
- Choosing the right pipe size ensures projects stay on track financially, balancing cost, performance, and regulatory requirements.
Choosing the right pipe size is crucial when planning any construction or plumbing project. For black iron (BI) pipes, size directly impacts material costs and installation, maintenance, and long-term performance. Selecting the wrong size can lead to inefficiencies, increased expenses, and potential system failures.
Understanding how pipe diameter, wall thickness, and length influence overall costs helps businesses and contractors make informed decisions. In this article, we’ll break down how pipe size affects the cost of black iron pipes. Read on to learn more.
Material Costs
The cost of raw materials is a major factor in manufacturing BI pipes, especially for larger sizes. Bigger pipes require more iron and steel, which naturally drives up production costs. For instance, a two-inch pipe uses significantly more material than a ½-inch pipe, making it more expensive to produce.
Beyond just size, raw material prices fluctuate based on global market trends, supply availability, and demand. When iron ore prices spike—whether due to supply chain disruptions or increased demand—manufacturers often have to adjust pipe prices accordingly. This is why understanding how pipe size impacts cost is crucial when budgeting for projects.
Manufacturing and Logistics
Larger pipes require more advanced machinery, longer production times, and precise welding techniques—especially for thicker-walled varieties. These factors increase both labor and energy costs, directly influencing the final production expense.
Labor is another key factor. Skilled workers are essential for welding, threading, and quality control, and as pipe size increases, so does the complexity of handling and assembly. This leads to higher labor costs per unit.
Logistics further drive up costs for larger BI pipes. Heavier and bulkier pipes demand specialized transport equipment, increasing shipping expenses. Additionally, longer distances between manufacturing plants and distribution centers result in higher fuel costs and extended delivery times.
Supply and Demand
When the demand for a specific pipe size is high, but supply is limited, prices naturally increase due to scarcity. Conversely, when supply exceeds demand, manufacturers may lower prices to move inventory more efficiently.
Commonly used pipe sizes, such as 1/2-inch and 1-inch black iron (BI) pipes, are produced in larger quantities, benefiting from economies of scale. This higher production volume helps keep costs lower. In contrast, larger-diameter pipes, which are less frequently manufactured, often have higher per-unit costs due to limited availability and specialized production requirements.
Market trends, construction projects, and industrial demands also play a crucial role in price fluctuations. For instance, a surge in large-scale infrastructure developments can significantly increase the demand for bigger pipes, leading to price hikes. Likewise, supply chain disruptions—such as raw material shortages or transportation delays—can limit availability and drive up costs.
Installation Costs
Larger pipes are heavier and bulkier, complicating handling and transportation. This requires more robust equipment, leading to increased rental or operational costs for cranes or forklifts. The installation process itself requires more labor. Tasks such as welding, threading, and securing pipes may need additional personnel, driving up labor costs.
When it comes to installation, Supreme Steel Pipe Corp. emphasizes the importance of skilled craftsmanship in both the manufacturing and installation processes. We assist with the installation, helping to manage labor costs based on the complexity of the pipe size.
Application Efficiency
The size of a pipe directly influences its flow rate, making it a critical factor in fluid or gas transport. Larger pipes accommodate higher flow rates, reducing friction and minimizing pressure loss. In contrast, smaller pipes create more friction, leading to greater pressure drops, which may require additional pumps to maintain efficiency.
Beyond flow rate, pipe size also affects durability. Larger BI pipes typically have thicker walls, enhancing their strength and reducing the need for frequent maintenance. While the initial cost of larger pipes may be higher, their long-term durability translates into cost savings by minimizing repairs and replacements.
Regulatory compliance is another key consideration. Our team ensures that all BI pipes meet Philippine National Standards (PNS), guaranteeing the highest levels of quality, safety, and performance for a wide range of applications.
Key Takeaway
Understanding how factors like pipe size affect the cost of black iron pipes is essential for keeping your projects on schedule and within budget. Discover quality black iron pipes at Supreme Steel Pipe Corp. We provide durable and reliable BI pipes designed for various industrial and construction needs. Contact us today to learn more about our products and specifications.