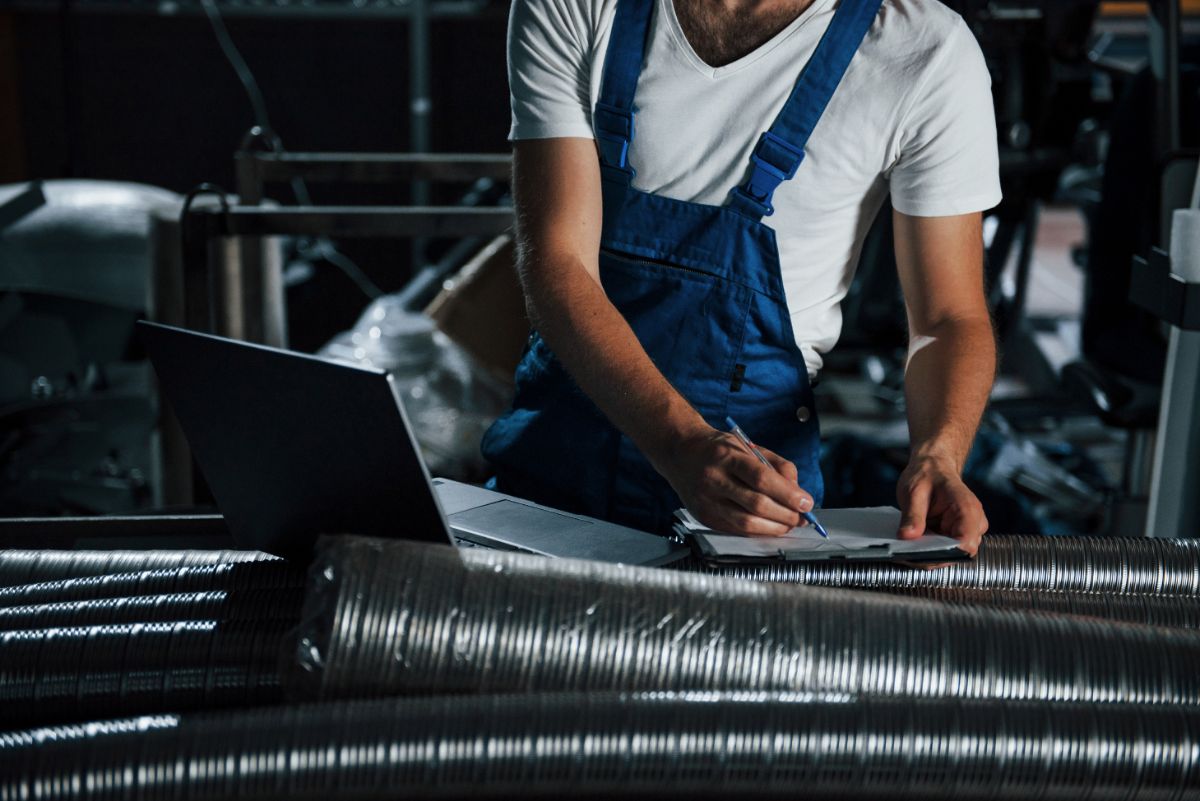
5 Types of Destructive Testing for Pipes
What are the types of destructive testing for pipes?
- Fatigue Testing
- Corrosion Testing
- Hardness Testing
- Residual Stress Measurement
- Tensile and Torsion Testing
When choosing any piping material, standards are very important. Without standards, pipes can end up compromising structural integrity and causing costly property damages. Though most desire quality pipes, not every pipe available in the market is created equally or with standards. This is knowing the different types of destructive testing is important.
Destructive testing can help identify which piping materials are better than others. This is done through a series of tests that deciphers how a pipe performs under pressure — damaging the pipe up to the point of failure.
When it comes to pipes, there are types of destructive testing that are considered and employed in order to identify the strengths, weaknesses, and breaking points. You can take these into account when choosing the right piping for a specific project or build. Continue reading on!
Destructive Testing vs. Non-Destructive Testing
Not all pipe testing methods are destructive. A less intense type of testing for pipes called non-destructive testing is also available. Destructive testing is considered the most reliable pipe testing method. However, non-destructive testing has some benefits over destructive testing because it saves on material costs. This is due to the fact that destructive testing requires that the piping material needs to be destroyed. Nonetheless, destructive testing is a more direct approach when it comes to figuring out a pipe’s strengths, weaknesses, and breaking points.
Below are the various types of destructive testing for pipes.
Fatigue Testing
This kind of pipe destructive testing is one that is conducted in an environment that simulates the material’s exposure to nature such as salt water and the open air. Fatigue testing focuses on how much the welded joints hold under unchanging or variable loads all while exposed to salt water and open air. It also tests to see the rate and extent of crack growth in pipes as well as in the zones affected by heat.
Corrosion Testing
Corrosion testing covers at what point and at what rate that smaller scale, aqueous corrosion – especially that derived from freshwater — occurs. At other times, this type of destructive testing also covers corrosion caused by saltwater.
Another variation of corrosion testing is one that covers piping materials that have corrosion risk due to their exposure to hydrogen. The thing is, hydrogen alongside stress can vastly increase the susceptibility to stress corrosion of different kinds of pipes. Sometimes, corrosion testing is carried out at varying temperatures.
Hardness Testing
Hardness testing is one of the most obvious and probably straightforward ways of testing the strength of steel pipes. It determines whether or not a component or part of a steel pipe goes through permanent deformation.
This destructive test in particular uses what’s called the Rockwell Scale of Hardness.
It indicates how much the pipe resists denting by examining the depth of penetration of an indenting material. Through harness testing, how hard a steel pipe is quantified.
In application, hardness testing will determine how well a steel pipe will hold up over time and how long it can be used effectively without it breaking.
Residual Stress Measurement
It goes without saying that stress and fatigue cause cracks and fractures all over piping material, especially during the same point time when both stress and fatigue are introduced. However, the effects of stress can go further than just when the fractures and cracks begin. That’s why residual stress measurement is an integral part of destructive testing when it comes to pipes.
This type of destructive testing measures how much of the effects of stress remain inside a solid material such as a steel pipe even after the original causes of stress are long gone.
Residual stress management is useful because engineers and designers will be able to take these measurements into consideration to determine in what manner the piping will be used and to what extent.
Tensile and Torsion Testing
Pipes can go through a lot. Tensile testing is a type of destructive test done by stretching and elongating a pipe lengthwise as well as in terms of girth in order to determine strength. The breaking strength, which is determined by when and how it reaches its breaking point, is measured to calculate how much force the pipe can withstand.
In addition to this, torsion testing, which derives its name from its meaning — to twist, is another method of destructive testing for pipes. Extreme twisting forces are applied to the pipe in order to determine the manner of shearing that it experiences up until it becomes totally deformed. As soon as the pipe is completely twisted, the failure point is defined.
Key Takeaway
As you can have read, there are different types of destructive testing for pipes. Each one is helping in evaluating the strength, weakness, and breaking point of a pipe. Thus, destructive tested pipes should be your purchasing standard!
Good thing that at Supreme Pipe, we have whatever steel pipe in the Philippines you need that will end up passing any type of destructive testing. Your project will benefit from our high-strength pipes that last for a long time. Browse the products of the most reputab;e steel pipe supplier in the Philippines here or contact us for other inquiries.