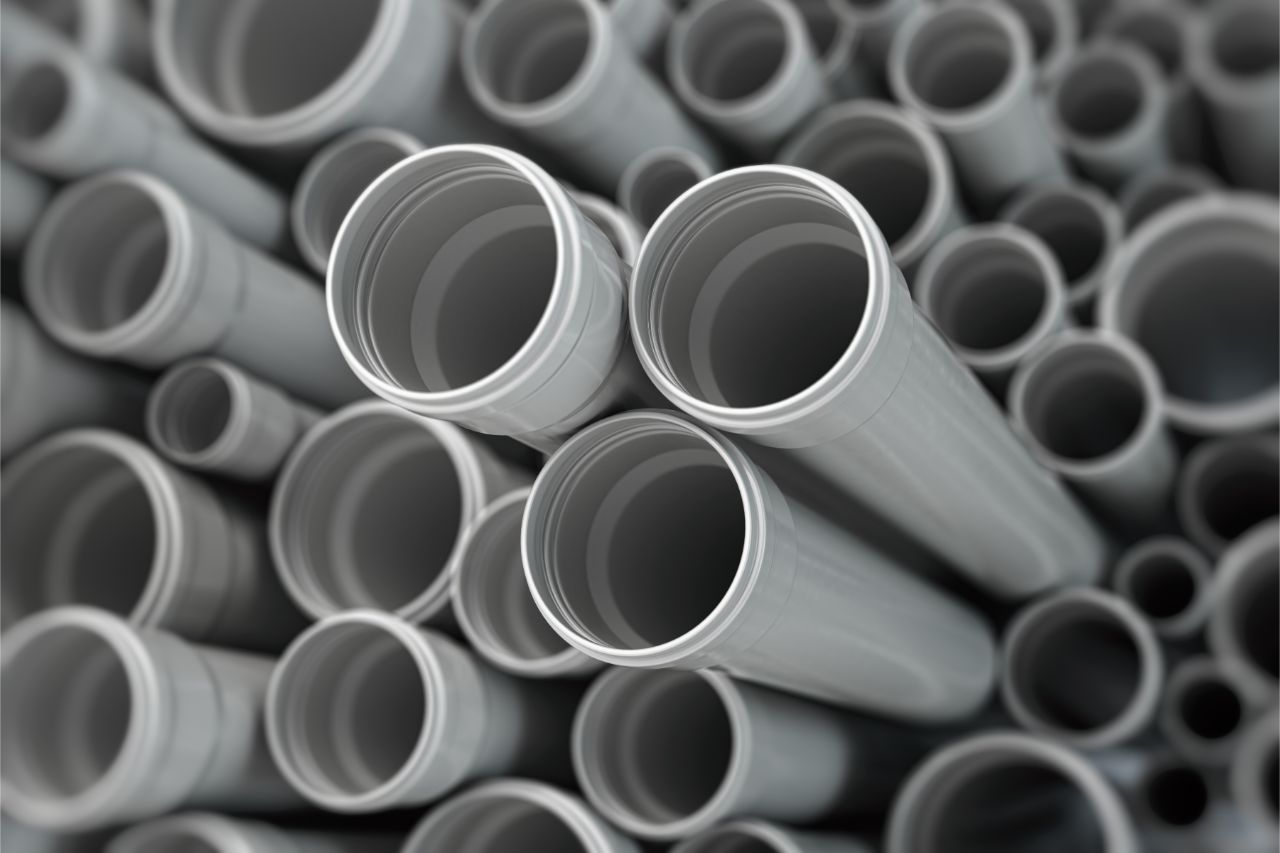
What is Destructive Testing? 7 Methods For Testing Pipes
What is destructive testing and what are some methods for testing pipes?
- Aggressive Environment Testing
- Corrosion Testing
- Fatigue Testing
- Hardness Testing
- Tensile Testing
- Hydrogen Testing
- Residual Stress Measurement
Knowing the strength of the materials you use is important across many industries. Especially for fields concerning big structures (like buildings, ships, space shuttles), you would have to be aware of how much strain each part can take before breaking. They are crucial in many calculations that are made for the safety of the people involved or the effectiveness of the structure. One way to know a material’s strength is through destructive testing. If you want to know what destructive testing is, keep reading below!
What is Destructive Testing (DT)?
Destructive testing consists of methods that you can do to test how a material’s performance and behavior. Considering the nature of these methods, the materials put to the test are often tested for failure. The procedures put the material under specific conditions, either depending on certain standards or service conditions. The results of the tests will show you how much the specimen can withstand until its failure.
These tests are often done in the lab using specialized equipment handled by experts such as engineers and scientists. DT methods can significantly affect an engineer’s critical assessments of a project. It is also good for failure investigation, materials characterization, and fabrication validation, and they are typically performed before a component or material is mass-produced.
Its counterpart is non-destructive testing, where, as opposed to DT methods, the specimen remains intact and useable after the procedure.
Destructive Testing Methods
The American Society for Testing and Materials (ASTM) is an international organization that has authority over testing and materials. They conduct studies and measure materials and determine specifications for a variety of products. The organization also offers standards and testing as part of its services, DT methods included. There are several destructive testing methods that experts use:
Aggressive Environment Testing
The materials that are being tested are usually expected to brave different kinds of environments once used. Aggressive Environment Testing determines the fatigue and fracture points of the specimen when under specific weather conditions. Factors that impact the materials include temperature, pressure, salinity, humidity, chemical exposure, and other corrosive natural forces. By mimicking the environment where it will be used, you’ll see how well a material will be able to perform.
Corrosion Testing
Somewhat similar to aggressive environment testing, corrosion testing figures out the corrosion point of a material when exposed to freshwater and seawater. As you can expect, this type of testing is done on materials that will most likely be exposed to aqueous corrosion like steel pipes.
Fatigue Testing
This DT method is used to test how much pressure, whether it be constant or variable amplitude loading, or strain a welded joint can take in open-air and seawater environments. The component will take as much fatigue as possible until it breaks, telling the scientists how strong welded parts or heat-affected areas of a structure can be.
Hardness Testing
The hardness of a material is its ability to resist deformation. It can also be used to determine how well a material can perform when under extreme stress. For this method, a Rockwell scale and an indenter are commonly used. The indenter will penetrate the material at a constant force, and the depth of penetration will show the hardness of the material.
Tensile Testing
This time, the material’s tensile strength is put to the test. The specimen will be compressed or elongated, depending on the test’s parameters, until it breaks or fails. The machine will apply controlled pressure on the specimen to measure its ultimate tensile strength, breaking strength, and maximum elongation or reduction.
Hydrogen Testing
Hydrogen is another element that can cause corrosion. That’s why there is a special DT method that measures how much hydrogen it would take before corrosion occurs in a material. As always, the parameters of the test would depend on the product, meaning the temperature and strain rates may vary.
Residual Stress Measurement
When a material experiences external stresses, sometimes internal stresses are still present when the cause of the external ones are gone. At times, these internal stresses can also affect surface stress. Scientists use complicated methods to accurately measure internal stress such as synchrotron diffraction, neutron diffraction, and x-ray diffraction. By testing for internal stress, engineers will be able to more accurately determine stress distribution throughout the material, which may affect the critical assessment of the structure.
Key Takeaway
Engineers, scientists, and quality experts all know how to properly test materials to ensure their strength. Now that you know what destructive testing is and what its methods are, you should know how important a material’s strength is. For example, if a steel pipe does not fit into the ASTM’s specifications, how would you know that it’s been tested and reliable?
Thankfully, at Supreme Pipe, we offer products that are tried and tested, not just in labs but in the field as well. With over 30 years of experience, we are one of the most trusted steel pipe suppliers in the Philippines. Contact us if you have any inquiries!