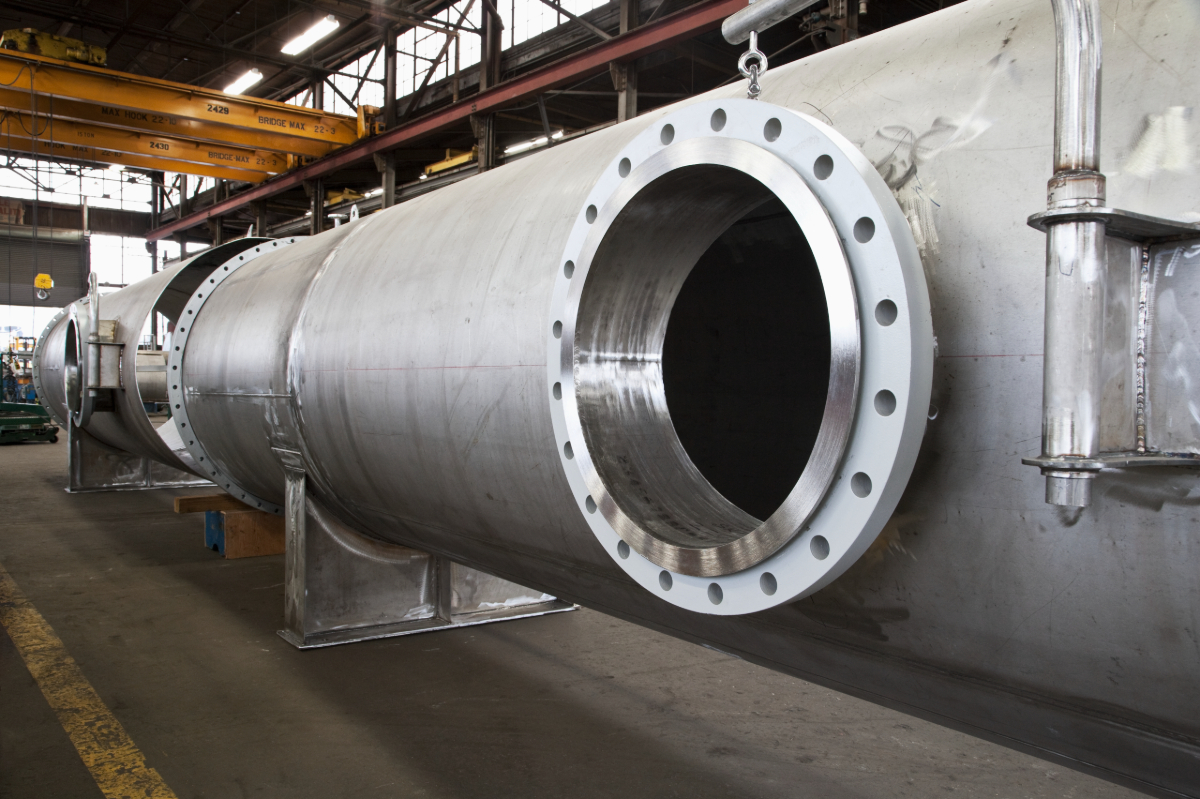
What Are Non-Destructive Testing (NDT) Methods?
What are some non-destructive testing (NDT) methods?
- Visual Testing (VT)
- Ultrasonic Testing (UT)
- Radiographic Testing (RT)
- Electromagnetic Testing (ET)
- Acoustic Emission Testing (AE)
- Leak Testing (LT)
Non-destructive testing (NDT), as the name implies, is the way to test materials, components, structures, or assemblies without having to damage them or affect their serviceability. This is as opposed to other methods of testing where the subject can no longer be used after the procedure. It has the obvious advantage of not losing materials when testing them, making it an efficient and cost-friendly process. But what are NDT methods exactly? How do you test something without destroying it?
Thanks to modern innovations, there is now a wide assortment of ways in which you can conduct NDTs, each with its parameters and degrees of success. Each method is different and can be better with certain types of materials. Below, you’ll find some of the most common non-destructive testing methods there are. Keep reading!
Visual Testing (VT)
Visual testing, or visual inspection, is the most common and basic testing method there is. It consists of an operator collecting visual data to determine the status of the material. An experienced worker will be able to see corrosion, damage, cracks, and other weaknesses from visual testing alone.
Oftentimes, inspectors use the naked eye to examine the material. Workers can also do this method with the help of technology and computer-assisted systems to do remote visual testing in hard-to-reach places.
Ultrasonic Testing (UT)
In ultrasonic testing, workers transmit high-frequency sound into a material to see changes in its properties. The sound waves’ interactions with the material provide clues to its overall status. This type of testing can be divided into three:
- Pulse Echo Inspection (PE): This method will transmit a sound wave onto a material’s surface. The time it takes for the sound to travel through the part and get reflected is recorded. If you know the material’s acoustic velocity, you will notice differences if there are discontinuities in the material.
- Through Transmission Testing (TT): This technique uses two transducers to test the material, one to transmit and one to receive. They are positioned on both ends of the test material and a sound wave is emitted. The sound is then reduced by any defects, like porosity, in the material.
- Time of Flight Diffraction (ToFD): When a true reflection can’t be obtained from a material, this method will be used. It measures diffraction in the sound caused by a defect on the surface. A good example would be catching defects along a perpendicular surface.
Radiographic Testing (RT)
This non-destructive testing method uses radiation to look for defects in a certain material. Radiographic testing utilizes x-rays for thin materials and gamma rays for thicker materials. These rays pass through the subject which is then processed into an image through the computer. This will reveal any imperfections that the material may have.
Electromagnetic Testing (ET)
Electromagnetic testing uses an electric current or a magnetic field to look for any defects in a material. They are applied to a conductive part of the subject and take note of any changes to make conclusions on the status of the material.
There are three types: eddy current testing, alternating current field measurement, and remote testing. Eddy testing uses an AC coil to induce a magnetic field, while the other two use a probe. Remote testing is best used to test pipes.
Acoustic Emission Testing (AE)
One of the more passive methods, acoustic emission testing, uses detection of ultrasound emissions to look for defects and discontinuities.
For example, active cracks within an assembly produce ultrasound bursts that the equipment can detect. This gives the inspector information on the integrity of the material. This method is used to test structures that are constantly under pressure such as bridges.
Leak Testing (LT)
This method is a way to spot leaks, cracks, holes, and other defects in materials like pipes. There are four ways to do this:
- Bubble leak test: This technique utilizes a tank of water, or sometimes a bottle of water, to look for leaks. The material is submerged into the water, and when bubbles form, that means air is escaping from it. The source of the bubbles shows where the leak is.
- Pressure change testing: This technique measures the pressure or vacuum in closed systems. Using the proper equipment, you can detect any changes in the pressure, which would indicate a leak.
- Halogen diode testing: This is similar to pressure change testing, except a halogen-based tracer gas is mixed with the air. A halogen tracer or “sniffer” is then used to detect leaks.
Mass spectrometer testing: In this variation, helium is used to mix with the air. The mass spectrometer or sniffer will detect changes in the air that would indicate a leak.
Key Takeaway
To be able to test materials and still use them after, the methods described in this article are great options. These are only some of the methods you can use for non-destructive testing. With this, you no longer need to ask: what are NDT methods?
If you’re looking for pipes that will pass any NDT method you subject them to, Supreme Pipe is where you find it! Take a look at our products on this page if you’re interested in high-quality steel pipes for your project. You can also contact us here if you have any inquiries.